蒸気システムの省エネルギー。うちの会社で可能なのか、何をしたらいいのか、どこをどう改善したらよいのか見当がつかないという企業も多いのではないでしょうか。
今回のコラムでは、基本的な蒸気システムを例に、省エネ対策における考え方と具体策をわかりやすく解説します。
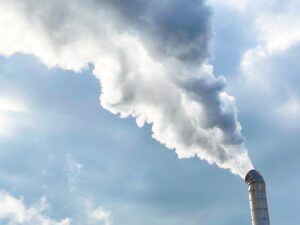
目次
1.省エネ&維持管理「二刀流の重要性」
蒸気システムの「省エネ」を考える場合、非常に大切になってくるのが「維持管理」の問題です。
省エネとは、現状でなされていないプラスアルファの新たなエネルギー削減といえます。
一方、維持管理は、適切に管理することなく失われている熱ロスというマイナスをなくし、ゼロに戻すことです。
つまり、無駄を省き効率を高めるうえで、省エネと維持管理は表裏一体のものです。
しかし、生産過程での蒸気の漏れや放熱の問題などは認識していても、生産に影響は出ていないので…と放置されていることが多いのも現実です。
省エネ対策を推し進めたとしても、維持管理を疎かにしたままでは効果も見えてこない、という結果にもなりかねません。
蒸気システムへの意識を高め、省エネ&維持管理の両輪で考えていくことが肝になってきます。
2. 正確な維持管理に欠かせない、精密な蒸気計測
ボイラで作られる蒸気のうち約20%〜30%は使われていないといわれています。
装置の放熱やスチームトラップ、バルブ、配管などからの漏れが主な要因です。
この行方不明蒸気を把握しておくことは、省エネを考えるうえで必須のものとなります。
蒸気流量計は多くの工場に備えられていると思いますが、この行方不明の「見えない蒸気」を見るためには、蒸気流量計の積算値管理とともに瞬時値管理が重要になってきます。
瞬時値を管理することで、プラント停止中に数字が出ていれば漏れや放熱を認知することができる、ピークロードが判明する、機器の異常を察知する、新規導入機器などの効果を数値化できる、など様々な情報を得ることができます。
そのためには、より細かな流量計測ができるレンジアビリティの高い計測器が必要となってきます。
国内ではレンジアビリティが1:10から1:15ほどのものが多く使われていますが、計測できる範囲が狭いためボイラから発生する蒸気量と各流量計の合算量が一致しないといった混乱が生じています。
より正確な情報を得てシステムの改善を進めていくには、瞬時値をより正確に管理できる「取りこぼしのない」流量計測と、そのための1:50から1:100といった高いレンジアビリティを持つ高精度な蒸気流量計が必須となってきます。
3. 蒸気システムの省エネ具体策
蒸気システムの省エネ対策を対象エリアごとに具体的に見ていきましょう。
ボイラ~加熱装置
自動送気システム
自動送気システムは省人化、メンテナンス費用の削減に寄与するものですが、最新の圧力トランスミッターを備えた自動送気システムでは、放熱をコントロールしつつ最低圧力を維持した送気も可能になりました。
短時間の送気停止後に加熱装置を再稼働させる際の時間の短縮、待機運転を含む長期のスケジュール管理などきめ細かなシステムの運用が可能になります。
スチームトラップ管理
ドレンを排出するスチームトラップは、定期点検していない場合の不良率が約30%なのに対し、年1回の点検を行っていれば不良率が5%ほどに低下するといわれています。
しかし、交換できるタイミングが限られる、交換しにくい場所にある、交換に時間がかかるなどの理由で適切に管理されていない場合が多くあります。
これらの問題を解消するのが、ボルト2本で容易にトラップ交換できる「ジョイントラ」です。
さらに、作業が容易なので現場のオペレーターが交換できる、配管サイズにかかわらず共用できるので在庫管理が容易になる、作動方式の異なるトラップへも交換可能など大きなメリットがあります。
グランド漏れ
バルブからのグランド漏れは、金銭的にも大きなロスとなります。
一般的な遮断弁の場合、口径や蒸気圧力、稼働時間によって変わってきますが、おおよそ年間で5万円から10万円ほどの損失になるというシミュレーションがあります。
このグランド漏れの悩みを解消するのが「ベローシール・バルブ」です。
ベローズを採用することにより、グランド部からの蒸気の漏れをシャットアウト。大きな省エネ効果をもたらします。
バルブの保温
蒸気システムにおけるバルブの数は相当数に上ります。
ひとつのバルブからの放熱は50Aグローブバブルで50A配管1.11m、50A減圧弁で50A配管1.55mに相当するとされています。
したがって、工場内のバルブを保温することは、想像以上に大きな省エネをもたらします。
バルブは消耗品であることを考慮し、保温材には脱着式のものが適しているといえるでしょう。
加熱装置からの排熱利用
ボイラで作られた蒸気エネルギーのうち26%は排出されています(0.7MPaGの場合)。
この排熱を回収し利用することで、大きな省エネ効果を得ることができます。
ドレン回収
高温のドレンを回収し、ボイラへの給水に利用することは省エネの基本といえます。
ボイラ給水温度が約6℃上昇すると、燃料1%の省エネが可能とされています。
例えば給水温度が15℃であったものがドレン利用で45℃になると、5%の省エネが達成できることになります。
さらに、ボイラ給水温度の上昇はボイラの蒸気発生量を増加させます。
現状のボイラ数のままで、全体の能力をアップさせることも可能になります。
ドレンは極めてクリーンな蒸留水です。ボイラ補給水に使用することで、ボイラブロー量を減らすことができます。
また、ドレンを捨てている場合には、ドレンという高温水を処理するための費用を削減することができます。
フラッシュ蒸気・廃蒸気回収
加圧された蒸気から生まれるドレンは、通常の100℃を大きく上回る高温になっています(0.7MPaGの場合170℃)。
これが一気圧の大気中に放出されると、一部は再蒸発(気化)します。
これがフラッシュ蒸気と呼ばれるもので、排出されるドレンのエネルギーのうち30%〜50%を占めます(0.2〜0.7MPaGの場合)。
この大きなエネルギーを持つフラッシュ蒸気(廃蒸気)を回収し、熱交換できる機器が「ベントコンデンサー」です。
廃蒸気の8倍から20倍の温水の製造が可能で、ボイラ給水の加温や産業用の温水などに幅広く活用することができます。
ベントコンデンサーは、食品関連企業などで使用されるスチーマーから出る温度の低い廃蒸気の回収も可能です。
スチーマーから排出される廃蒸気は多少なりとも製品の成分が混じっているため、これまで熱回収の対象と考えられてきませんでした。
しかし、ベントコンデンサーの登場により、ボイラ給水加熱での利用が注目されています。
また省エネ効果に加え、屋外へ排出される湯気を抑えられることで、工場近隣の住環境への配慮という課題を達成できることにも関心が高まっています。
4. まとめ
蒸気システムの省エネにおいては、省エネ対策とともに維持管理との両面作戦が効果的であることを見てきました。
省エネのはじめの一歩は「問題はあるけど、とりあえず生産はできているから」という、無関心をやめることから始まります。
新出光では蒸気システムに関する様々なソリューションを提供しております。ぜひ、お問い合わせ・ご相談ください。
また、今回のコラムに関してご意見や掲載してほしい話題などがございましたら、お問い合わせフォームよりお知らせください。